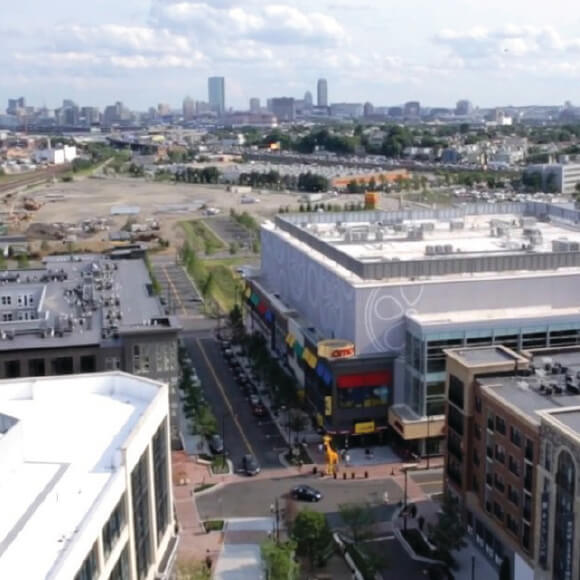
Assembly Row, Blocks 1-4 and 10
Geopier Rammed Aggregate Piers® (RAPs) were installed below footings and slabs-on-grade throughout the 5-story structure.
- General Contractor 1: Avalon Bay Communities, Inc
- General Contractor 2: Cranshaw Construction
- Geotechnical Engineer: Haley & Aldrich, Inc
- Structural Engineer 1: McNamara/Salvia, Inc
- Structural Engineer 2: LeMessurier Consultants
Assembly Row is a mixed-use development constructed on a 10-block city site. Surrounded by a six-acre riverfront park, Assembly Row houses approximately 2,100 residential units, a luxury hotel and 2.25M square feet of office and retail space.
The construction site contained unsuitable urban fill, loose estuarine deposits, soft organic soils and a relatively high groundwater table.
The Geopier Grouted Impact® system allowed for traditional shallow footing and slab-on-grade construction which helped expedite the construction schedule. The rigid inclusion system was used to limit total and differential settlement to less than 1 inch and ½ inch and provided a maximum allowable footing bearing pressure of 6 kips per square foot. More than 6,000 rigid inclusion elements were installed throughout Blocks 1-4 and 10. Goepier's grouted piers were used to support footings and prevent pier bulging within the organic soil layer, while non-grouted RAPs were used to support slabs-on-grade. To address the close proximity of the bottom of footing elevations to the soft organic soil layer, the designer engineered a structural fill pad (“footing pad”) beneath the footings to help transfer footing stresses to the grouted piers and surrounding matrix soil. A test footing supported by four grouted piers underwent a full-scale modulus test to 200% of the grouted pier element design stress. In addition, five individual grouted pier modulus tests were performed to 200% of the grouted pier element design stress.